Inflation Reduction Act: Sourcing materials and making batteries are challenging

With the passage of the Inflation Reduction Act (IRA) — the most significant climate change policy passed in our country to date — engineers, like myself, are at the center of developing and deploying the clean energy technology in record time. Importantly, these technologies include the batteries for electric vehicles (EVs), a centerpiece of the legislation and long-time foundation of strategies to reduce harmful greenhouse gas emissions. The IRA lays out some tough — and dramatic — engineering challenges for EV batteries.
For example, scaling up battery production in the U.S. is a cornerstone of the IRA. In it, EVs receive a tax credit only if their batteries meet certain criteria. According to the bill, in just six short years, receiving a tax credit for an EV would require its entire battery to be manufactured domestically. Yes, the Tesla Gigafactory is a household name, and there are a handful of other large plants across the country. But families in China already are able to choose from more than 90 battery gigafactories to discuss around their kitchen tables. Europeans have about 20.
It is far easier to buy a battery made abroad. We can’t change this reality without engineers as the heroes in what will be a dramatic build out of battery manufacturing in the United States.
Potentially even more challenging than building the facilities that assemble battery parts is acquiring all the materials they contain. Metals — including lithium, copper, manganese, nickel and cobalt — are a key part of what makes a battery work.
However, the U.S. is not a dominant producer of any of these metals. And, typically, countries that produce metals don’t manufacture battery components or batteries at all. A common example is Chile, which produces 25 percent of the world’s lithium, but no appreciable number of batteries. About 70 percent of our cobalt comes from the Democratic Republic of the Congo (DRC), and 15 to 20 percent of that is mined by hand. This cobalt is generally exported to China, where it is used in battery production. The social and environmental costs of cobalt mining in the DRC have been documented by many organizations, including Amnesty International and in my own research and are the subject of government efforts to improve conditions.
Recognizing the supply chain risks that such an international supply chain entails, the IRA sets targets for the percentage of the value of critical materials in a battery that come in total from domestic mines recycling, or from countries with which the U.S. has a free-trade agreement. This target hits 80 percent in four years. Given that most batteries are assembled outside the U.S., the amount of U.S.-mined metals incorporated in batteries today is incredibly small. To increase this percentage so dramatically in the next four years, advances in recycling existing lithium-ion batteries is key.
Subject to intense research and development, this technology is very young and not operated yet on a large scale in the U.S. Previous research has estimated that accomplishing a target of about 8 percent lithium and 12 percent each of nickel and cobalt by 2030 would be possible. By mass, this is only about one-third of the critical materials in a battery that would be achieved in eight (not four) years. Again, engineers must come to the rescue to design and scale these processes.
Another route to advancing toward this target will be to increase domestic production, including through mining — although this would take more than four years to accomplish in a way that meets the targets in the IRA. Again, engineers would be at the forefront of developing and operating mines. However, there is a long history of environmental and social challenges associated with mines.
News stories have addressed concerns with, for example, increasing lithium mining on Indigenous lands in the United States. If engineers construct or expand mines, they will need to work respectfully and responsibly with local communities, including Indigenous communities that have experienced terrible historical injustices over land rights.
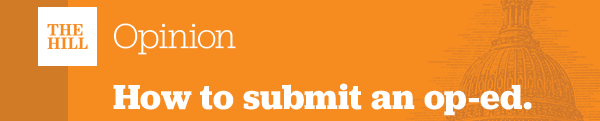
We don’t want to reduce greenhouse gas emissions from vehicles only to pollute culturally important lands that also offer ecosystem services like carbon storage. Scaling up battery production is a systems-level problem. We need the systems-level thinking of engineers — working closely and respectfully with communities — to get this right from the outset.
To be sure, many professions will support the realization of the IRA. But we should encourage every student to be a part of the excitement and consider an engineering career. Those of us at universities need to also do our part to provide an interdisciplinary education that extends beyond the engineering school to encompass social sciences, humanities and the arts. Such richly-trained engineers will be ready to responsibly develop and deploy the clean energy technologies we need to address climate change without causing harm to — and ideally even benefitting — the communities involved in its development and deployment.
Jennifer Dunn is an associate professor of chemical and biological engineering at Northwestern University and the co-director of Northwestern’s Center for Engineering Sustainability and Resilience.
Copyright 2023 Nexstar Media Inc. All rights reserved. This material may not be published, broadcast, rewritten, or redistributed.