In baby formula shortage, poor quality control is to blame

The ongoing shortage of baby formula is a crisis of huge proportions for many American parents. Though this seems like another pandemic supply chain issue, the root of this problem is major issues and oversights in quality management. Over the past few days, several revelations have surfaced regarding the “shocking conditions” inside the Abbott Nutrition plant that manufactures these products and whose closure prompted the widespread crisis — from bacteria growth to standing water to roof leaks to inadequate hygiene. The Food and Drug Administration (FDA) has said the plant cannot reopen until Abbott takes hundreds of steps to fulfill the requirements needed to comply with U.S. food safety standards.
Though the closure of Abbott’s Michigan plant triggered this crisis, it’s clear that this is not the only cause for the widespread shortage. A supply chain for one product cannot and should not depend on one plant unless the industry is highly concentrated. And indeed, this is a highly concentrated market with only four manufacturers — Abbott, Mead Johnson Nutrition, Nestle USA, and Perrigo — supplying 90 percent of the domestic baby formula market in the U.S. Abbott alone has a 40 percent share of the U.S. market, and the currently shuttered Michigan plant was responsible for 40 percent of the company’s U.S. production.
Still, we shouldn’t be here.
Yes, the government acknowledged it should have shut down the Michigan site long ago. Standing pools of water and roof leaks don’t emerge overnight; they are persistent issues that likely were observed in previous visits. In fact, based on a whistleblower’s report received in October 2021, “active efforts were undertaken and even celebrated during and after the 2019 FDA audit to keep the auditors from learning of certain events believed to be associated with the discovery of micros in infant formula at the Michigan site.” So yes, while the FDA conducted lax inspections, Abbott Laboratories, Abbott Nutrition’s parent company, bears much of the blame.
Though the FDA regulates Abbott Laboratories, and thus Abbott Nutrition, the companies also should have been self-regulating. That evidently wasn’t happening. Either senior managers at Abbott Laboratories knew about the quality issues at the Michigan plant and did nothing, or they were completely unaware that the issues existed. To be honest, I’m not sure which situation is worse.
If they knew and did nothing, it’s likely criminal negligence for which they should be held accountable. If they were unaware, it doesn’t make it all that much better. The fact that something like this was happening for so long, with egregious violations needing hundreds of corrective actions, indicates a pervasive cover-up culture and relaxed attitude toward quality and safety.
Surely this cannot be an issue in only one plant. It’s also probably not an issue unique to Abbott Nutrition. When we see problems of this type, it’s usually the tip of the iceberg, meaning it could be happening in the plants of other baby formula manufacturers. For appalling issues to happen — regarding both quality and the reporting of problems — there must exist a deep culture that cultivates such behavior. When this happens, each day that a CEO still has a job, company shareholders basically are saying they support such a culture.
When I teach lean operations, I discuss “quality at the source.” The idea is that even if high quality is not your main competitive strategy, you want to pay attention to quality issues at every possible level, and in every possible stage of the value chain, because correcting them at a later stage will have significant costs and reputational implications.
Abbott must figure out how such a situation arose in the first place. In fact, they should temporarily shut down all their plants and conduct a root cause analysis of how such a culture was allowed to prevail for so long.
Abbott isn’t the first firm that has an apparent culture of cover-ups; there were similar issues at Boeing, for example. Though baby formula and aerospace seem vastly different, they both operate in highly regulated, highly concentrated industries.
Quality, like resilience, is something that costs money in the short run but pays off in the long run — but unless there is a deep competitive pressure or risk of shutting down, firms typically prioritize the short run. This is what happened at Boeing, where engineers raised concerns about quality issues and, because it was a local monopolist, management reportedly chose to overlook the warnings.
Of course, it’s much cheaper to build a low-cost supply chain, reduce the number of quality inspections and corrections, and pray that nothing happens. Since 2017, Abbott has had only five recalls across all its products — two of which triggered the current shortage. How is it possible there were so few recalls when there are now such serious violations being noted?
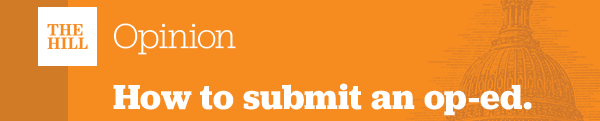
There’s just not enough competitive pressure to punish companies that allow defective or life-threatening products to be released in the market. This is driven by tough regulations on new entrants and decisions that create market concentration, followed by relaxed regulations once the products are in circulation. This push and pull results in less pressure on companies to be their own careful quality and safety controllers.
With baby formula, government actions that were meant to simplify the management and/or handling of these products resulted in the creation of a brittle supply chain, ultimately causing more harm than good.
Gad Allon is faculty director of the Jerome Fisher Program in Management & Technology at the University of Pennsylvania. Follow him on Twitter @g_allon.
Copyright 2023 Nexstar Media Inc. All rights reserved. This material may not be published, broadcast, rewritten, or redistributed.